Processing Technology and Application of Expanded Fish Feed
Floating Fish Feed Making Machine
Processing Technology and Application of Expanded Fish Feed
According to the feeding characteristics of different aquatic animals, such as river crabs and other benthic animals, they are used to looking for food in the water bottom and adopt a slower feeding method. In this way, the feed particles needed can not be too hard and strong, and the loss caused by small debris in the process of feeding should be minimized. From this point of view, the expanded sediment feed is more suitable: the expanded sediment pellet feed is easy to absorb water and soften, suitable for gnawing, can also reduce the loss of debris generated during gnawing, reduce feed waste and water pollution. Moreover, the extruded feed has long water resistance and high maturity.
Twin-screw wet extruder is widely used in the production of extruded feed. There are many factors affecting material expansion, but they are closely related to conditioning conditions, operation conditions of expander and material properties. The sinking and floating of expanded feed can be controlled by changing extrusion conditions.
1. The effect of conditioning is particularly important in the production of sunken puffed feed. The strong effect of extrusion should be weakened and the effect of conditioning should be strengthened in the production of expanded sediment feed. When tempering, water and steam are added, and enough tempering time is needed to soften and ripen the material sufficiently, so as to create conditions for the material to achieve better plasticity in the weaker conditions of the expansion chamber in the next step. In this way, the material will continue to ripen, without producing a larger degree of expansion, to obtain sediment feed. Adequate conditioning can improve feed digestibility, water resistance and extrusion stability, that is, homogeneity of the product.
2. The extruded sediment feed should adopt lower screw speed, which can provide the required extrusion and shearing effect without excessive pressure, and avoid the sharp increase of material energy. It is not easy to become sediment feed because of the excessive degree of expansion after the die hole.
3. The control of barrel temperature is another important aspect of material energy control. In the feeding section of the expander barrel, in order to ensure the good conveying performance of the material, it can not be heated; in the melting section of the barrel, it must be heated, and the barrel temperature is 120-125℃, which should not be too high. The screw and barrel can shear and knead the material to promote material maturation and improve plasticity; in the homogenizing section of the barrel end, the barrel should be cooled (barrel temperature 40-50 C), which has been reduced. The energy possessed by the ripening plastic material reduces the supersaturation of water in the material, so that when the material is extruded from the die hole into the atmosphere, it will not oversize.
회사 :
주소 :
전화 :
Email :
Skype :
Whatapp/Wechat:
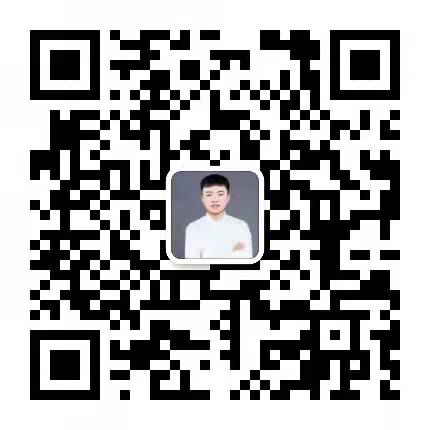